Mastering metalworking requires a blend of technical understanding, practical skills, and stringent safety measures. This article provides a comprehensive exploration of basic and advanced techniques, essential tools, and safety precautions.
By delving into the intricacies of this craft, readers will gain a solid foundation to effectively navigate the complex landscape. Whether you’re a novice or a veteran, this piece will enhance your skill set and elevate your proficiency.
In This Post
Understanding Basic Concepts
In the realm of metalworking, mastering the fundamental concepts is paramount to achieving technical proficiency. This includes understanding properties, forming processes, and analysis.
A comparison of different types reveals varying properties such as strength, malleability, conductivity, and corrosion resistance. These properties dictate their suitability for different applications. For instance, copper’s superior conductivity makes it ideal for electrical wiring, while steel’s robustness renders it perfect for construction.
Understanding the fundamentals of welding, a widely metal-forming process is also crucial. Welding involves the coalescence of metals using high heat to melt the parts together, facilitating the creation of robust joints. Mastery of this process is essential for producing durable and effective structures.
Essential Tools
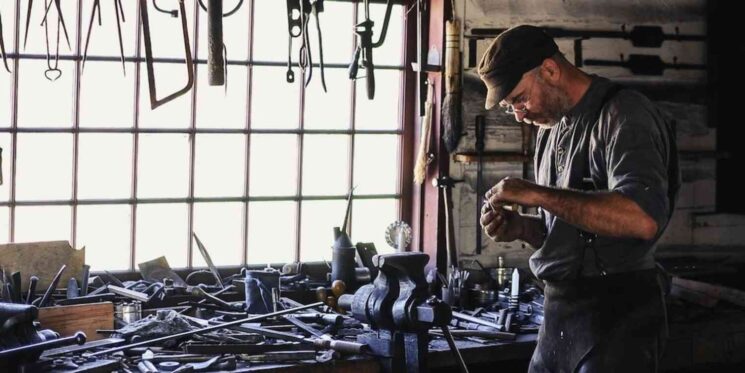
One must be equipped with a variety of essential tools to effectively engage in metalworking. This requires careful selection of quality equipment, which should be robust and durable to withstand the rigors of the task. Key tools include but are not limited to hammers, anvils, files, and drills.
Metalworking technical know how each tool serves a specific function, and understanding their purpose is critical to successful metalworking. Concurrently, tool maintenance essentials should not be overlooked. Regular cleaning, proper storage, and timely sharpening are imperative to ensure longevity and operational efficiency.
Investing in high-caliber tools and maintaining them judiciously not only enhances the precision and quality of the metalwork but also ensures safety. Thus, mastery is significantly reliant on these two aspects.
Mastering Metal Shaping Techniques
Frequently mastering the art of shaping necessitates understanding and applying a range of technical techniques with precision. This sphere, often referred to as Metal Shaping Artistry, demands a profound comprehension of materials, tools, and Innovative Shaping Techniques.
Key procedures include stretching, shrinking, bending, and doming. Stretching, for instance, requires precision and control to extend the surface area without distortion. Shrinking techniques, conversely, condense the metal, often using a specialized shrinker tool. Bending reshapes the metal around a set axis while doming molds it into a convex shape.
These techniques each contribute to a broader skill set, pivotal for producing intricate, high-quality pieces. The mastery of these techniques is an essential stepping stone towards impeccable Metal Shaping Artistry.
Safety Measures
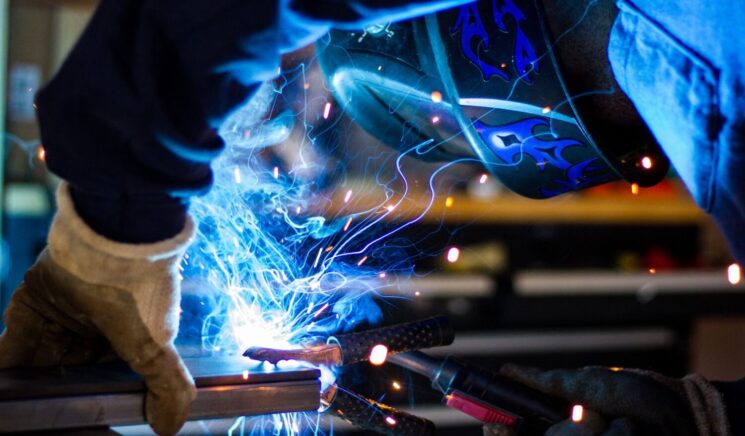
Adopting stringent safety measures is paramount when engaging in metalworking, as it is characterized by several potential hazards that can result in severe injuries if not properly addressed.
The first step is hazard identification: this involves analyzing the work environment for any potential risks, including sharp edges, hot surfaces, and flying debris. Once identified, these risks must be mitigated using appropriate protective equipment.
This includes safety glasses to shield the eyes from sparks, heat-resistant gloves for handling hot metals, and steel-toe boots to protect the feet from heavy objects. Furthermore, respirators are crucial to guard against inhalation of harmful fumes.
Regular training on equipment handling and emergency response strategies further enhances safety in this environment.
Advanced Skills and Practices
Despite the inherent complexities, acquiring advanced skills and practices is essential for mastery of this technical domain. This involves understanding welding intricacies and alloy selection, both critical in crafting durable and efficient products.
Concerning welding intricacies, precision is key. Mastery of different welding techniques such as MIG, TIG, and stick welding requires diligent practice and an understanding of safety protocols.
Alloy selection, on the other hand, necessitates a comprehensive knowledge of metallurgy. Different alloys possess varying properties, and the choice of alloy significantly affects the final product’s characteristics like strength, corrosion resistance, and ductility.
Therefore, mastering these advanced skills is a prerequisite for successful metalworking.
The Role of Digital Technology
As this industry evolves, digital technology plays a critical role in enhancing efficiency, precision, and creativity in various processes. Understanding how digital tools integrate with traditional techniques is crucial for modern workers.
Embracing Computer-Aided Design (CAD)
Computer-aided design (CAD) has revolutionized it by allowing intricate designs to be meticulously planned and visualized before physical work begins. CAD software enables workers to create detailed 3D models of their projects, facilitating precision and reducing the likelihood of errors during production.
The Impact of CNC Machining
Computer Numerical Control (CNC) machining represents a significant advancement. This technology involves the use of computers to control machine tools, such as lathes, mills, and grinders. CNC machining offers unparalleled accuracy and repeatability, making it indispensable for producing complex parts with tight tolerances.
Integrating 3D Printing
3D printing, or additive manufacturing, is increasingly being used for prototyping and production. This technology allows for the creation of parts with complex geometries that would be difficult or impossible to achieve with traditional methods. It also reduces waste by using only the necessary material to build a part.
Frequently Asked Questions (FAQs)
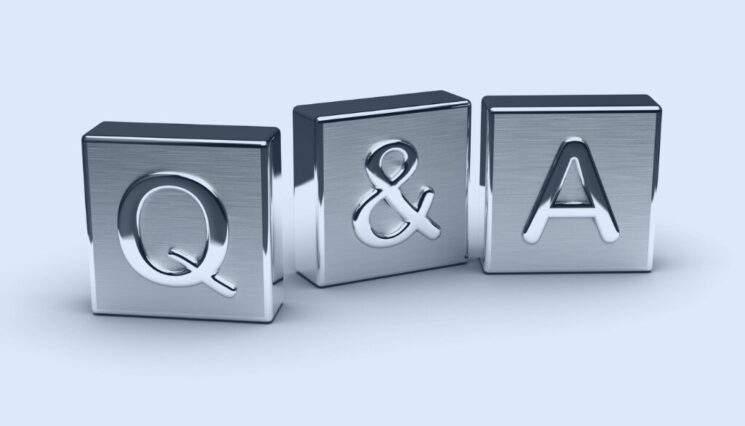
What Are Some Common Career Paths in this Industry?
Common career paths in this industry include fabrication, machining, welding, and metalworking apprenticeships. These roles require essential skills such as measuring, cutting, shaping, and joining parts.
How Has Metalworking Evolved Over the Years in Terms of Technology and Techniques?
Technological advancements have drastically reshaped the industry. Techniques have evolved from manual hammering and forging to precision CNC machining, improving accuracy, and efficiency, and expanding the design and production possibilities.
What Are Some Examples of Masterpieces Created?
In terms of Metalworking Masterpieces Appreciation, several artistic interpretations exist. For instance, the Eiffel Tower, the Statue of Liberty, and the Gates of Paradise exhibit exquisite skills and creativity.
What Are the Environmental Impacts and How Can They Be Mitigated?
Metalworking’s carbon footprint is significant due to energy-intensive processes and waste generation. Sustainable practices such as recycling, energy efficiency, and cleaner production can mitigate these environmental impacts.
Are There Any International Standards or Certifications for Professionals?
Yes, numerous international standards and certifications exist for professionals. These include ISO 9001 for quality management, highlighting the benefits of certification and the impact of standardization on the industry’s best practices.